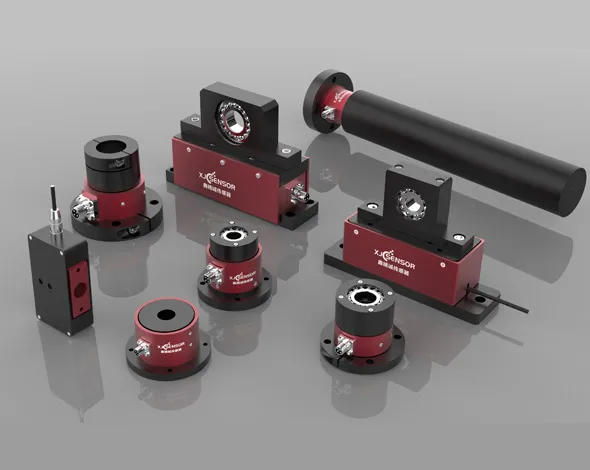
Demystifying Static and Dynamic Torque Sensors: Understanding their Applications and Differences
Torque measurement plays a crucial role in various industries, ensuring accurate assessment of rotational forces. In this blog post, we delve into the world of static and dynamic torque sensors, exploring their applications, differences, and how they contribute to precision measurement and control. Join us as we unravel the intricacies of these essential sensors and their impact on diverse industries.
Static Torque Sensors
Static torque sensors are designed to measure torque in stationary or fixed conditions, where there is no rotational movement involved. Key features and applications include:
Design and Operation
Static torque sensors consist of strain gauges mounted on a shaft or applied directly to the torque-inducing element. They measure the strain caused by the applied torque, converting it into an electrical signal for precise measurement.
Applications
Static torque sensors find application in torque monitoring and control systems, quality control processes, fastening operations, material testing, and research and development.
Benefits
These sensors offer high accuracy and resolution, making them ideal for tasks that require precise measurement and control of torque values in static conditions. They enable validation of torque specifications, ensuring proper assembly and preventing over-tightening or under-tightening scenarios.
Dynamic Torque Sensors
Static torque sensors are designed to measure torque in stationary or fixed conditions, where there is no rotational movement involved. Key features and applications include:
Design and Operation
Dynamic torque sensors use strain gauges integrated into rotating elements, such as drive shafts or spindles, to measure torque in real-time. They provide continuous data during rotational motion.
Applications
Dynamic torque sensors are integral in applications like automotive and aerospace testing, manufacturing equipment, robotics, engine and powertrain testing, and performance analysis.
Benefits
These sensors allow for accurate monitoring of torque fluctuations during dynamic movements, enabling performance analysis, optimization of power transmission systems, and detection of abnormal torque conditions.
Differences between Static and Dynamic Torque Sensors
While both static and dynamic torque sensors serve the purpose of measuring torque, they differ in their design and applications:
Operating Conditions
Static torque sensors measure torque in stationary or fixed conditions, while dynamic torque sensors capture torque data during rotational or dynamic movements.
Measurement Outputs
Static torque sensors provide precise measurements for stationary torque values, while dynamic torque sensors offer continuous monitoring and measurement of torque fluctuations during rotational motion.
Applications
Static torque sensors excel in scenarios requiring accurate torque control and measurement in assembly processes, quality assurance, and material testing. Dynamic torque sensors are vital in industries that involve rotational equipment, such as automotive testing, robotics, and performance analysis.
Static and dynamic torque sensors are indispensable tools for precision torque measurement across various industries. Understanding their unique characteristics, applications, and differences allows engineers and researchers to select the most suitable sensor for their specific needs. Whether it’s ensuring proper fastening in assembly operations or analyzing rotational forces in complex machinery, static and dynamic torque sensors contribute to improved efficiency, performance, and safety in numerous industries where accurate torque measurement is paramount.
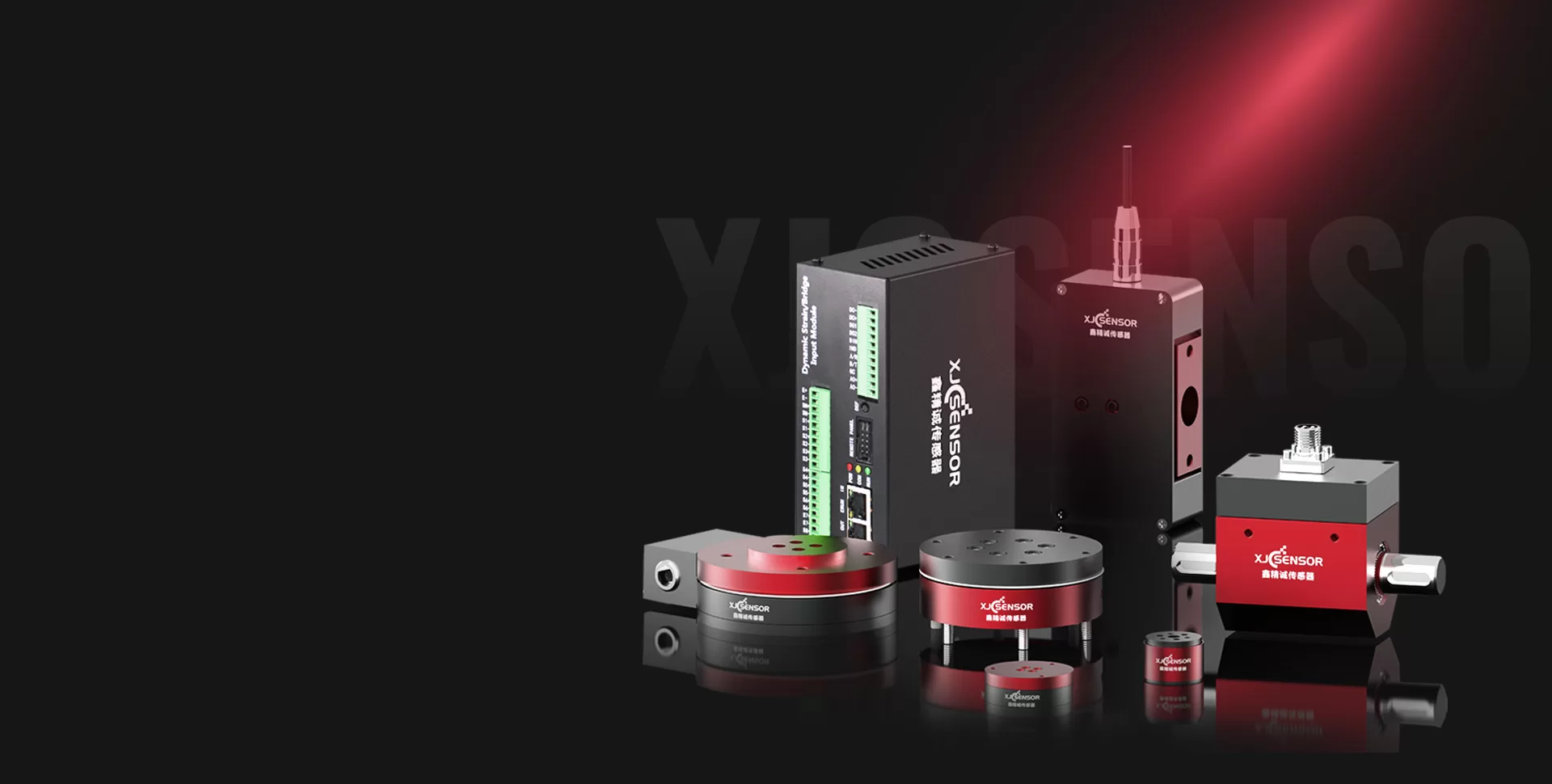